Every project requires management of many elements, including—but not limited to—files, budget, schedule, communication, risk, and quality management. Every project also lives within a quality management system (QMS) that complements
the project and facilitates successful project completion. QMS is the framework that includes policies, procedures, and processes required for consistent planning and execution of products or services.
As far as the risk and quality management elements of the QMS, risk management involves careful assessment of positive and negative risks, and then developing a strategy to address those risks. For the purpose of this discussion, the focus is on negative
risk. Managing negative risk in a project requires an assessment of the probability of the risk occurring and the potential impact if it does occur.
Depending on results of the risk analysis, there are four standard ways to address negative risk, one of which overlaps into quality management.
- Avoid the risk altogether by not pursuing the work or by requesting a change to the scope or statement of work.
- Transfer the risk to a specialized partner or subcontractor.
- Accept the risk because the probability of the risk occurring and/or the impact if it does occur is minimal.
- Control the risk through some form of QMS risk mitigation activity.
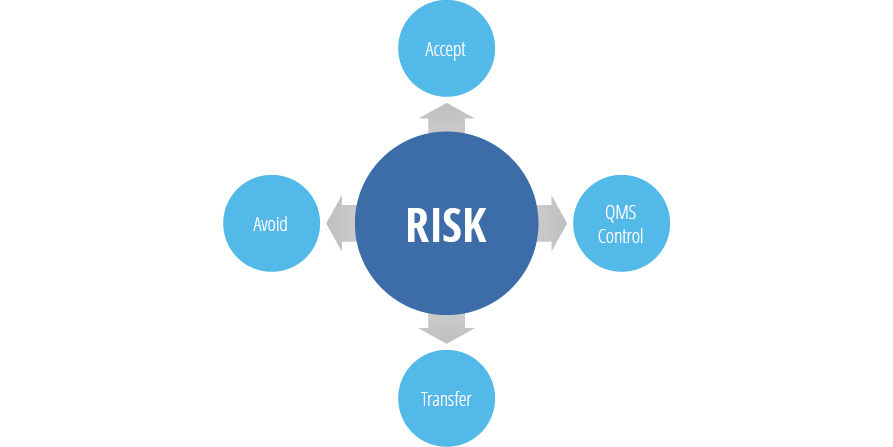
Controlling or mitigating the risk through QMS tactics can take many forms, including, but not limited to:
- Enhancing the knowledge management system used on the project to ensure all team members have easy access to controlling guidance and standards. Project and task managers and all members on the project team shouldn’t need to struggle
to find controlling guidance and standards.
- Creating clear production checklists and/or standard operating procedure. Building quality in rather than inspecting it in should always be the goal. Why? Because rework is often time consuming and expensive.
- Identifying strategic locations in the workflow to independently validate compliance with contract requirements, and how those reviews should be conducted. It is never good practice to end-load inspections; again, rework is time consuming
and expensive.
- Creating prescriptive quality control checklists to be used by independent inspectors. These checklists should include clear evidence that all quality control citations were properly addressed and should strive to focus on core elements
of the project and less so on stylistic elements.
So what is the difference between risk management and quality management? Simply put, they complement each other. If we choose not to accept, avoid, or transfer the identified risk, the risk response may leverage one or more tactics, including several
from the QMS toolbox, such as the four noted above.